Why Plastics Rotomolding is Ideal for Custom-Made Plastic Items
Why Plastics Rotomolding is Ideal for Custom-Made Plastic Items
Blog Article
Pockets rotomolding, or rotational molding, is a manufacturing method that has acquired immense recognition for the power to make resilient, hollow elements with exemplary precision. From big industrial tanks to little custom parts, this technique is known for their versatility and efficiency. Below, we'll investigate the important thing advantages of Plastics Rotomolding and why it's develop into a chosen alternative for making top quality, empty parts.
What is Materials Rotomolding?
Rotomolding is a production process that requires heat plastic material inside a rotating mold. This permits the molten plastic to fur the inside materials of the mold consistently, making useless elements with an easy structure. The effect? A product that's not just resilient but also very versatile, giving countless programs across industries.
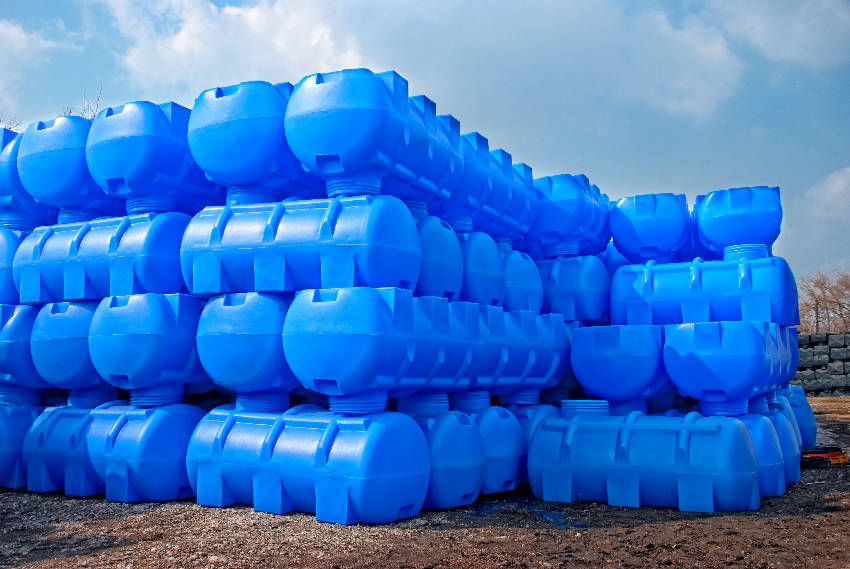
Essential Advantages of Parts Rotomolding
1. Energy and Durability
One of many standout benefits of pockets rotomolding may be the unparalleled durability it offers. Rotomolded pieces are made to tolerate serious situations, including large affects, severe temperature, and chemical exposure. That energy makes rotomolded components perfect for programs in industries like automotive, agriculture, and construction.
The smooth, single-piece structure also plays a part in the architectural reliability of rotomolded products. Unlike other practices, there are no stitches or weak points, lowering the risk of pauses or leaks.
2. Cost-Effective Production
Rotomolding is extremely cost-effective, especially when creating large or complex useless parts. The method involves relatively minimal tooling costs compared to other production practices, such as for instance procedure molding or strike molding. This causes it to be specially suited to small-to-medium creation runs without reducing quality.
Furthermore, the capability to make pieces with consistent wall width decreases substance spend, optimizing cost-efficiency actually further.
3. Design Freedom
The flexibility of rotomolding opens the doorway to highly custom-made designs. Whether it's elaborate shapes, undercuts, or different wall thicknesses, rotomolding allows producers to show actually the absolute most complex styles into reality. That freedom is important for industries that demand accuracy and flexibility inside their components.
More modification options include textured materials, embedded inserts, and even multi-layered parts for added insulation or strength.
4. Lightweight Yet Robust
Rotomolded areas achieve the right balance between weight and durability. The worthless structure minimizes substance usage, ensuring products stay lightweight while sustaining their structural strength. This really is especially beneficial for components such as for example outdoor gear, tanks, or playground structures, where easy transportation and installment are critical considerations.

5. Eco-Friendly Production
Rotational molding is also commonly celebrated for its environmental benefits. The procedure effects in little material waste, as plastic resources may often be recycled or recycled. Furthermore, manufacturers may use eco-friendly materials to align with sustainability goals. This jobs rotomolding being an increasingly desirable selection for companies seeking to cut back their environmental impact.
Why Parts Rotomolding Stands Out
Plastics rotomolding has revolutionized the manufacturing of sturdy, useless parts by offering a unique combination of strength, price performance, and style flexibility. By leveraging this technique, companies can offer high-quality parts that meet the particular needs of varied industries while encouraging an eco-conscious approach to production.
If you are buying production process that offers seamless toughness and irresistible precision, rotomolding could be the answer.
Report this page